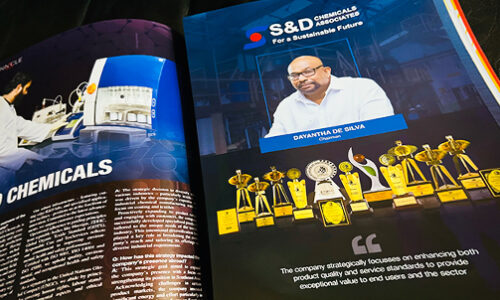
Chairman of S&D Chemicals speaks to LMD Magazine
This article was published on LMD | Sri Lanka Business Magazine on 27th December 2023 https://lmd.lk/sd-chemicals/ Q: Can you give us an overview of the …
The Bluesign standard is a comprehensive Input-Stream-Management-System that covers all Environmental, Health and Safety (EHS) aspects along the textile manufacturing chain. Moreover, the bluesign standard is based on five principles namely,
• resource productivity
• consumer safety
• air emissions
• water emissions
• occupational health and safety
In addition, product stewardship is undertaking the responsibility for manufactured products and the reduction of the EHS impacts of a product.
In the path taken to achieve product stewardship and the bluesign system partnership, we S & D Chemicals through an Integrated Management System (IMS), have undertaken the sole responsibility to meet the requirements enforced by bluesign that covers the implementation of the input stream management, process management and quality control, monitoring traceability and hazard communication.
Raw materials obtained from reputable suppliers are initially tested and analyzed for quality and the presence of hazardous substances or impurities. All data on raw materials inclusive of SDSs obtained from respective suppliers, are made available to the relevant personnel in order to ensure proper and safe handling, storage and occupational health and safety. At S & D Chemicals, the execution of the software based Raw Material HazMat Control System, aids to control the input of raw materials at the initial stage of the production process, which complies with the MRSL (Material Restricted Substance List) and BSSL (Bluesign Substance List). Therefore, through the use of this control system, the entry of hazardous substances into the production process is controlled.
Risk management is implemented by training employees to undertake appropriate and safe handling, storage and disposal measures, usage of appropriate personal protective equipment (PPE), and preparing for emergency situations. Moreover, internal audits are conducted on an annual basis, when a risk assessment and an environmental impact assessment (EIA) is carried out. In these assessments, non-conformities are identified and corrective measures that need to be taken are planned, implemented and monitored so as to enable continuous improvements to be made. Standard operating procedures (SOPs) are prepared wherever appropriate and are made available to the respective personnel.
At the production phase, the use of sophisticated analytical equipment (e.g.: ICP, GCMS, HPLC and the FTIR Spectrophotometer) in the inhouse accredited laboratory, aid to test various production parameters at identified frequencies, thereby enabling the analysis of product quality and the detection of the presence of any hazardous substances or impurities in the desired, finished products, which also complies with BSSL. Hence, the key objective of the bluesign standard, which is to produce non-hazardous finished products are met with. In addition, a systematic approach of implementing the interim labelling of products ensures the proper packaging and storage of finished products.
A comprehensive management system is maintained, which allows any finished product or intermediate product to the relevant raw material batch number to be tracked down. Therefore, in the event a customer or quality reject arises, the entire history of the product can be traced and the cause of the issue could be identified and hence addressed.
Classification and labelling of the products is performed in accordance with the Globally Harmonized System (GHS) (UN GHS Rev 6) and the Classification, Labelling and Packaging (CLP in EU (European Union)). SDSs for each of the individual products that complies with the GHS and the CLP are prepared and checked by relevant, experienced personnel.
Hence, through the implementation of the IMS, which is in accordance with ISO 9001, ISO 14001 and OHSAS 18001 standards, all materials and production processes are controlled and monitored to ensure occupational health and safety, resource productivity through the facility’s reduced energy and water consumption, environmental cleanliness through the facility’s reduced emissions to the environment, optimized product quality and achieving compliance with local and international legislations.
In conclusion, the requirements enforced by bluesign were fulfilled and the bluesign system certification was achieved through the achievement of the bluesign system partnership. Furthermore, in the near future as a bluesign system partner, we strive towards achieving product certification, i.e. the bluesign approval for various, identified individual products that are manufactured at S and D Chemicals.
https://www.bluesign.com/industry/chemical-suppliers/references.html
This article was published on LMD | Sri Lanka Business Magazine on 27th December 2023 https://lmd.lk/sd-chemicals/ Q: Can you give us an overview of the …
In the recently held Achiever Awards 2023, organized by the Ceylon National Chamber of Industries in partnership with the Ministry of Industries, S and D …
The Presidential award is the grandest recognition that a foreign exchange earner could achieve. Earning this is an honor, and S and D Chemicals (Pvt) …
S & D Laboratory has been awarded ISO 17025 accreditation from Sri Lanka Accreditation Board (SLAB) in August 2019. This accreditation, along with the ISO …
The latest approaches in denim manufacturing reveal sustainable solutions, which undoubtedly would benefit not only the producer and the consumer but also the planet. Both …
As most of you know, Indonesia International Textile & Garment Expo is the largest event in the textile and garment industry of South East-Asia. Indo …